News and opinion from the industry
Construction management
2,000,000+ projects worldwide
Helping the largest construction companies in the world more easily manage their job sites.
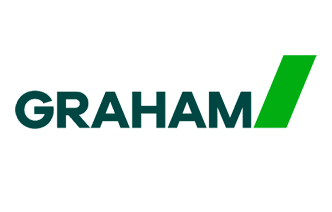
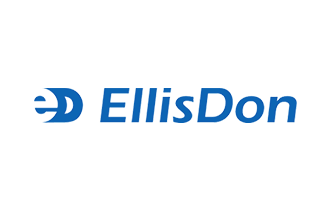
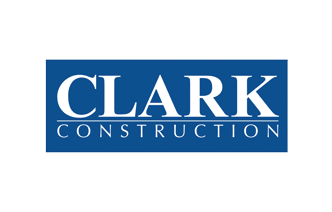
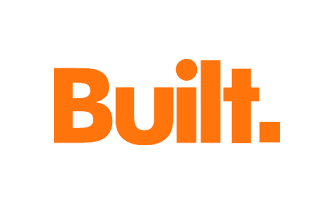
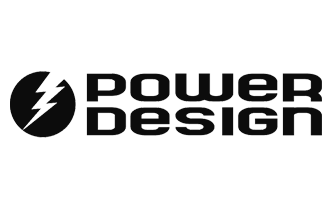
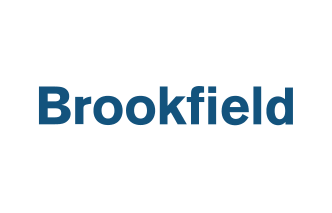
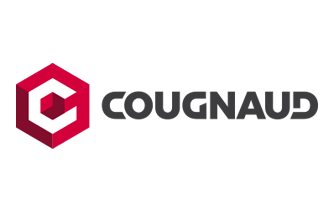
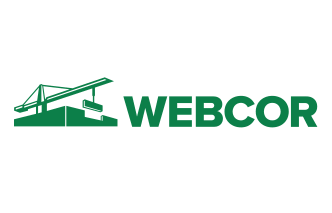
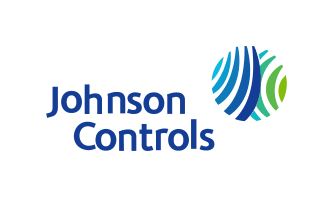
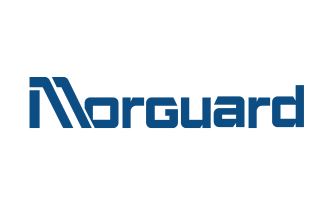
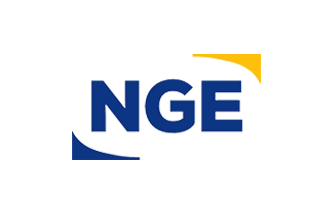
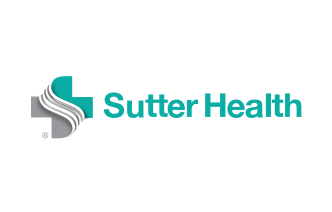
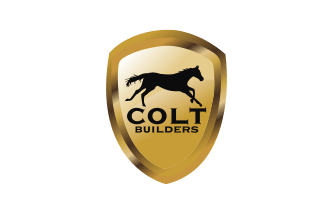
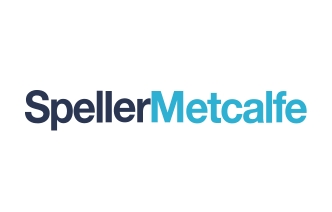
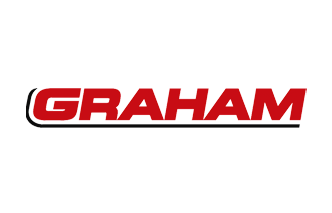
News and opinion from the industry
Helping the largest construction companies in the world more easily manage their job sites.