Trusted news and resources for builders
Fieldwire Blog
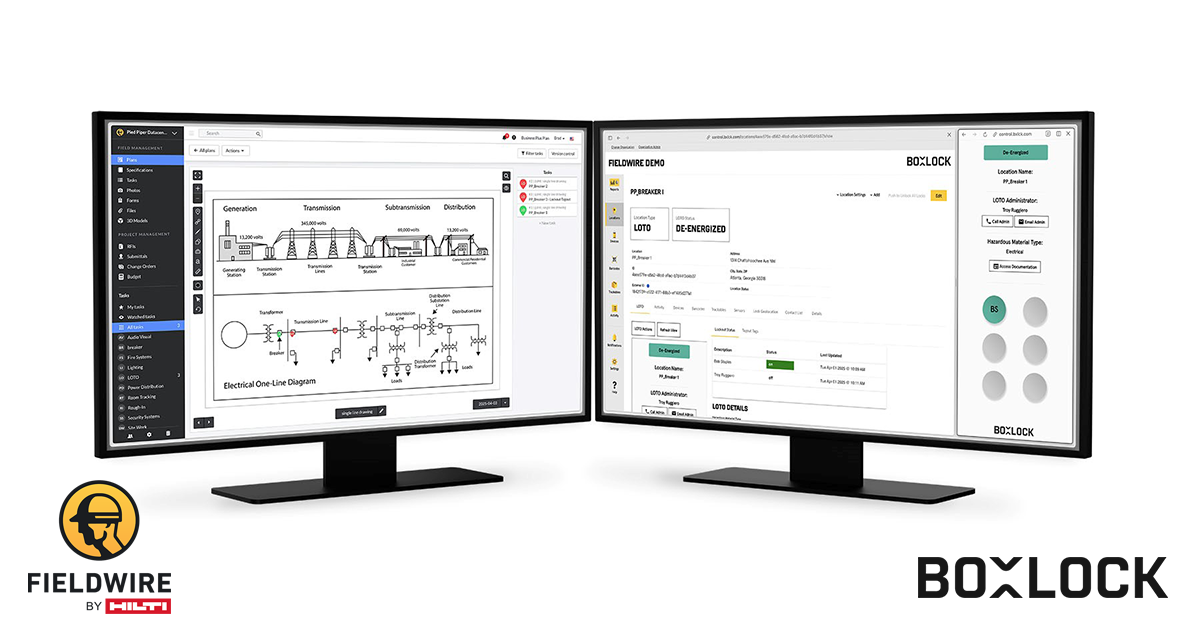
Fieldwire by Hilti and BoxLock introduce real-time integration for lockout tagout (LOTO) on single-line drawings
May 7, 2025
The new Fieldwire and BoxLock integration bridges the gap in field to office communication by combining physical lockout tagout (LOTO) with the digital drawings crews...
2,000,000+ projects worldwide
Helping the largest construction companies in the world more easily manage their job sites.
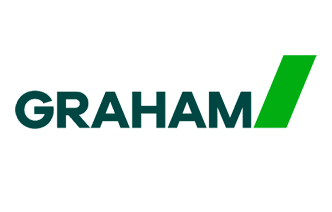
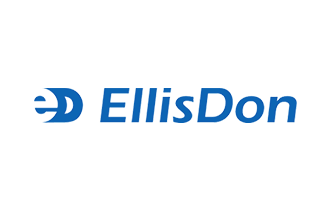
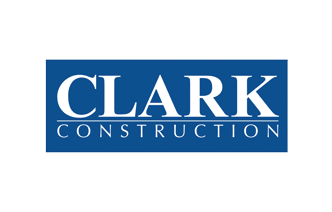
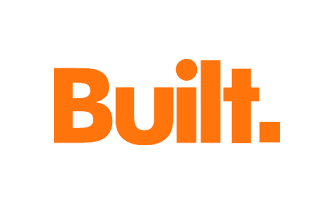
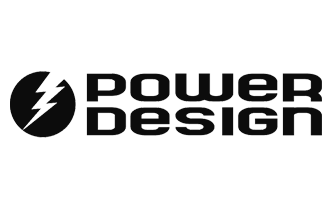
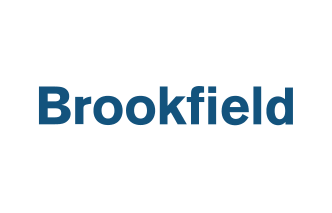
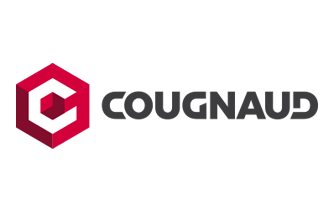
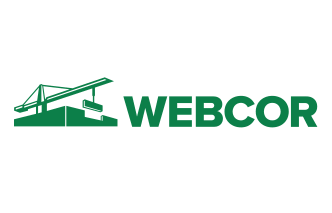
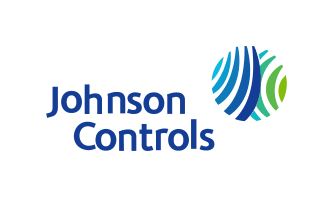
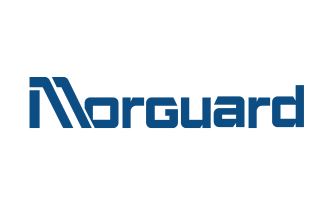
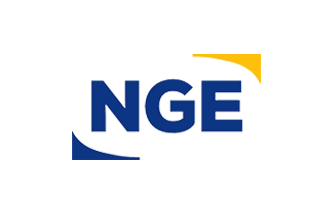
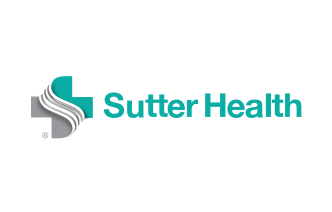
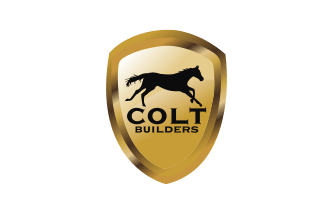
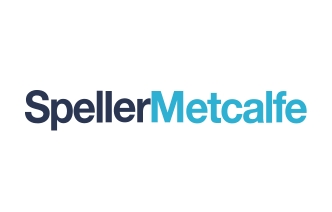
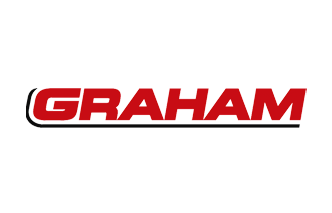